Steel Rail Standards
In the world there are some important standards about steel rail, on which we must pay the most attention. As a steel rail manufacturer, we advise you buy railroad rail on the basis of steel rail standards.
ASTM A1-00 standard
ASTM A1-00 is the first standard established by American Association for testing of materials for the technical conditions of steel rail. The current edition is issued in 2000.
American Rail Engineering Maintenance Association (AREMA)
American Rail Engineering Maintenance Association (AREMA) is the highest authoritative organization in the US in the field of rail technical conditions. The standard can better reflect the requirements of heavy haul rail on steel rail, including Version 1993, Version 2002 and Version 2004.
Soviet / Russia standards of steel rail
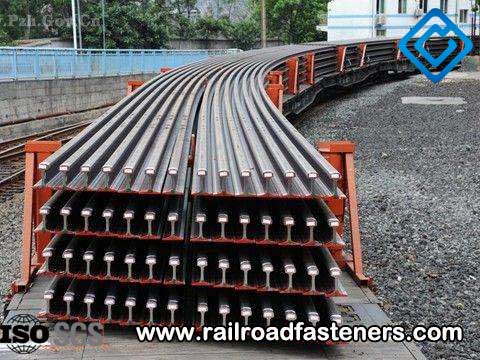
- A. ГOCT 24182-80: hot rolled steel rail (Soviet standard)
- B. ГOCT 18267-82: heat treated steel rail (Soviet standard)
- C. ГOCT P 51685-2000: major changes have been revised in it. (Russia standard)
Japan standards of steel rail
- A. JIS E1101 (1993, 2001): hot rolled steel rail
- B. JIS E1123: end heat treated steel rail
- C. JIS E (1120-1994): heat treated steel rail
The technical requirements of Japan steel rail are not high, but the products of steel rail are very high in quality.
International Union of Railways (UIC)
The eighth edition of technical conditions for rail delivery (UIC860, 1986.7):
This standard is one of popular standards of steel rail. Many countries are using this standard in international bidding procurement of steel rail. But because of the changes of work focus of UIC, it has no longer made the formulation and revision of standard of steel rail. Obviously, the UIC standards issued in 1986 cannot meet the technical development of railway and metallurgical production progress nowadays.
Europe standards of steel rail: EN13674-1:2003 (E)
In November, 1994, the draft of standard has been proposed. In February, 1996, the second draft has been made. In 1998, the third is published. In 2000, it is finally identified. It is issued in 2003 formally. The standard reflects overall requirements of steel rails for high-speed railway, which is one of the world's most advanced and strictest standards. In the standard, the specified usage range in technical conditions is clear for high speed railway. The standard series issued by China are made based on the reference to it together with taking into account actual domestic development.
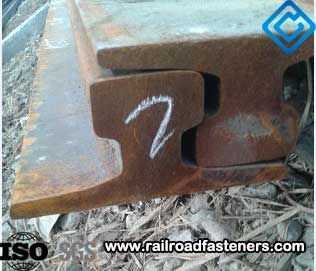
Europe standard for turnouts
Here is PrEN13674-2:2003 (E). This standard specifies the requirements for European rail switches and turnouts.
Steel Rail Production
The traditional production technology of steel rail can be roughly divided into three parts: smelting, rolling and finishing. In the past, steel rail was made by the methods of open hearth smelting, mould casting and groove rolling. So in the respects of steel purification and geometric dimensions it was not good and satisfying. The modern production process of steel rail mainly includes refinery smelting, refinery rolling and finishing and refinery finishing. Under automatic detection and long production, steel rail quality has more greatly improved than that before.
Modern production technology of steel rail
A. Billet production
In modern production of steel rail, refinery smelting and continuous casting process has been adopted by people. The process includes: Pre-desulfuration of raw iron——LD converter smelting——Slag disposal——LF external furnace refining——Vacuum degassing——Continuous casting. By means of pre-desulphurization, external furnace refining and vacuum degassing, the steel is clean. Continuous casting can not only increase metal yield, but also improve the quality of the billet.
B. Rolling, finishing and quality inspection of steel rail
The rolling process of steel rail includes: Continuous casting billet——Reheating furnace——De-scaling by high pressure water——Being rolled by universal rolling mill——Heat pre-bending of steel rolling——Composite straightening——Flatness detection——Eddy current testing——Ultrasonic testing——Visual inspection—— Sawing, end finishing——Storage.
The reheating furnace can make the billet uniformly heated. The multistage high pressure water de-scaling can ensure the surface quality of the steel rail. The universal rolling technology can ensure dimensional accuracy of the steel rail. These are the sign of modern production of steel rail. The heat pre-bending technology can reduce residual stress and straightening noise.
C. Quality inspection of steel rail
About quality inspection, people usually adopt the centralized arrangement, including flatness laser automatic inspection, eddy current testing, ultrasonic testing and the surface quality visual inspection and so on.
Nondestructive detection technology (NDT) is an important part of maintenance work of rail products in the protection of railway line and transportation safety, which plays an important role in railway transportation. The NDT work are main crucial detections, including rail inspection, turnout inspection and welding inspection, etc. basically by the method of ultrasonic flaw detection.
Ultrasonic testing (Ultrasonic Testing, referred to as UT) is one of the most widely used nondestructive testing methods whose essence is mechanical wave. The mechanical vibration and transmission of the particle constitute the basis of physical theory of ultrasonic flaw detection. The ultrasonic transmission process can be divided into two parts: first, geometric acoustics referring to the law of reflection, refraction law and waveform conversion law. It mainly includes the path of acoustic beam and the defection location. Second, physical acoustics touching on superposition, interference, diffraction and Huygens principle mainly includes the distribution of sound pressure and quantitative defection and so on.
The flaw detection system of steel rail includes the inspection of new steel rail and inspection of steel rail in use.
The new rail inspection is mainly performed in rail production plant. Generally, the multi channel automatic testing equipment will be used for testing. The inspection of steel rail in use can only be done at the track scene. People mainly use small rail flaw detector (rail inspection car). This kind of flaw inspection car for steel rail generally have 5 to 8 channels with 5 to 8 different types of probes and perfect alarm function. It can be implemented on a rail or land and put into use at the time of railroad clearance. It is the main equipment for rail flaw detection. With the development of railway transportation and train speed increasing, the traffic density is increasing as well. The car is more and more difficult to be used. Thus, the application of larger inspection car has been gradually developed. Now the basic form of flaw detection becomes the combination of small car and large car with the implementation of the mode of periodic detection.